Medical Device- Hardware Development
Why TechFlex-Dev for your Medical Device Hardware Development

Surgical Robot
Comprehensive Expertise in
Medical Device Design
TechFlex has a robust foundation in medical device design, as highlighted in our core project.
Our team of engineers and specialists possess deep knowledge and experience in developing advanced medical devices that meet stringent industry standards.
Clients can trust that TechFlex will deliver innovative and reliable hardware solutions tailored to their unique needs.
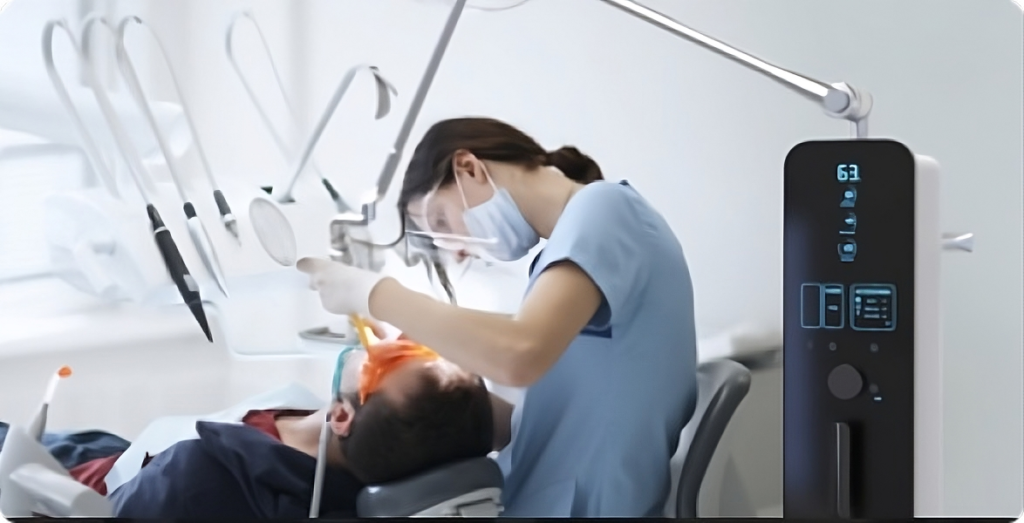
Specialized Engineering Support
One of the critical sub-tasks in our hardware solution is the Hardware Engineering.
Our engineering team is adept at tackling complex challenges and translating client requirements into practical, efficient designs. We utilize cutting-edge technologies and methodologies to ensure that every hardware component is optimized for performance, safety, and regulatory compliance. This engineering prowess ensures that our clients receive top-tier solutions that enhance the functionality and reliability of their medical devices.

Streamlined Production Support
In addition to engineering, TechFlex offers comprehensive “(Hardware) Production Support.” This service ensures that the transition from design to manufacturing is seamless and efficient. Our New Product Introduction (NPI) team works closely with clients to oversee the manufacturing process, identify potential issues early, and implement solutions that maintain the integrity and quality of the hardware components. This level of support minimizes delays and reduces the risk of costly errors, ultimately accelerating the time-to-market for our clients’ devices.
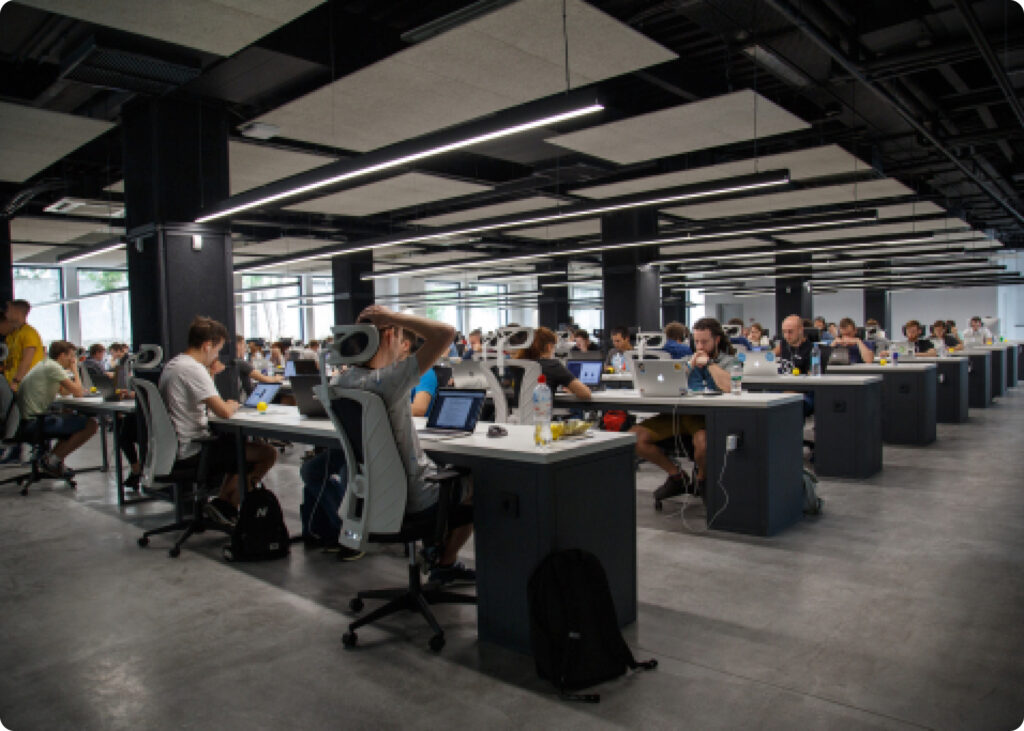
Rapid Prototyping Capabilities
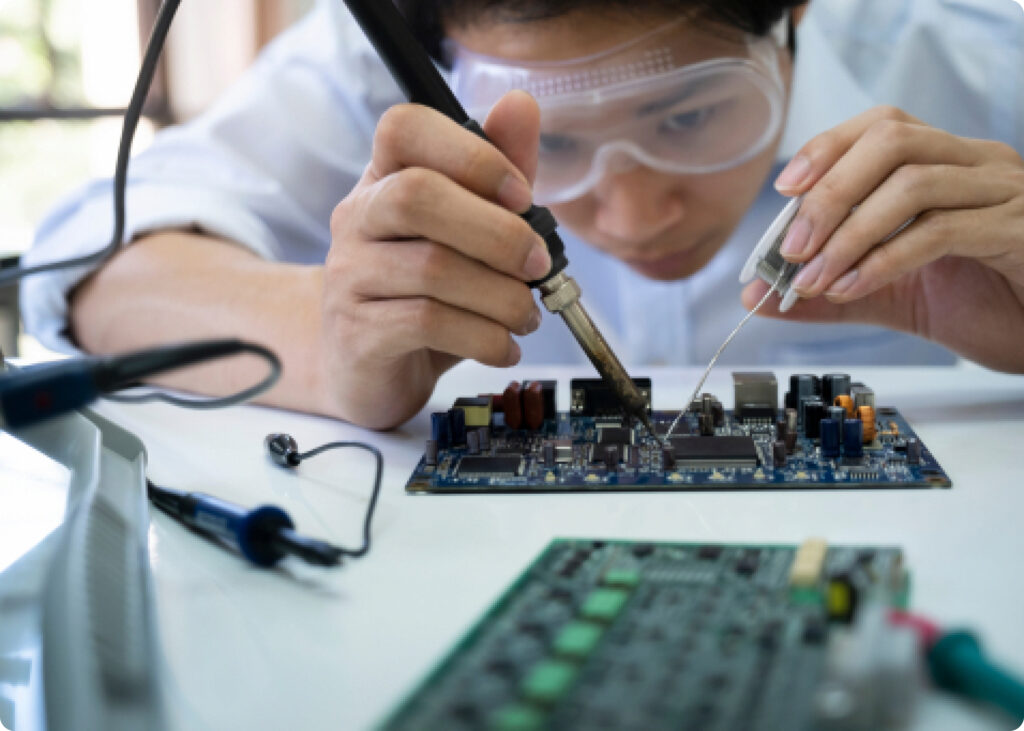
Collaborative Approach
At TechFlex, we believe that collaboration is key to successful medical device development. We work closely with our clients throughout the entire project lifecycle, from initial concept to final production. Our team values open and frequent communication and actively involves clients in the decision-making process. This collaborative approach ensures that the final hardware solution aligns with the client’s vision and meets their specific requirements.
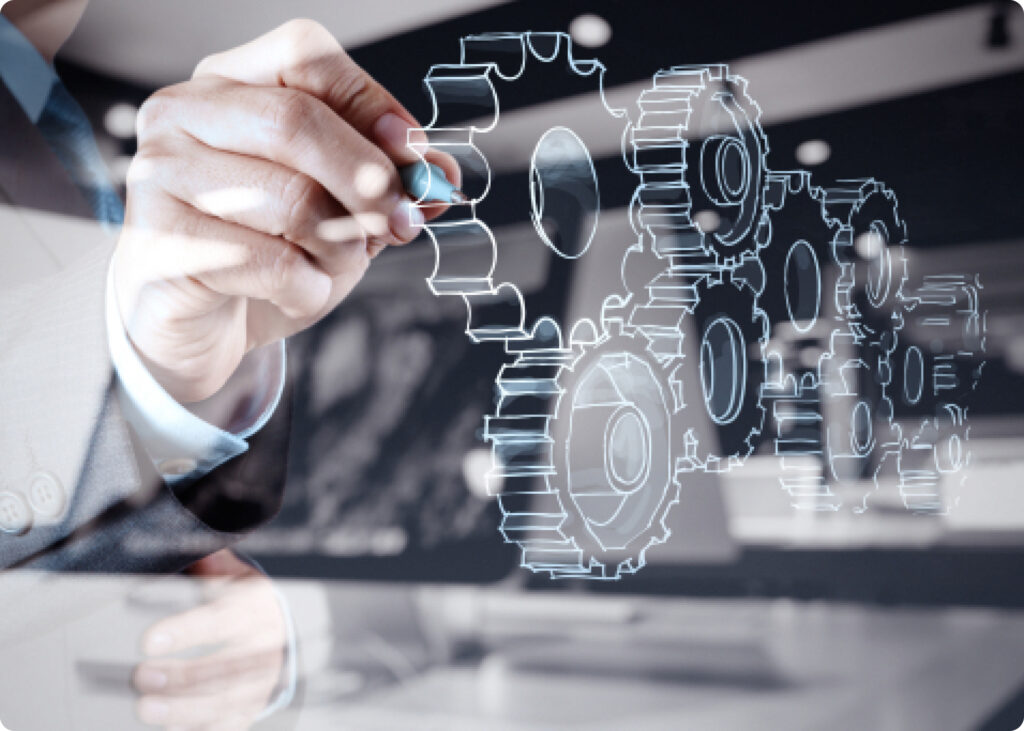
Regulatory Compliance and Quality Assurance
Medical devices are subject to rigorous regulatory standards to ensure their safety and efficacy. TechFlex is well-versed in these regulations and incorporates compliance considerations into every stage of the hardware development process. Our quality assurance and regulatory team meticulously reviews each component and system to ensure they meet all relevant standards and guidelines. This commitment to regulatory compliance gives clients confidence that their devices will pass necessary inspections and certifications.

Cost-Effective Solutions
Developing high-quality medical device hardware can be expensive, but TechFlex is committed to providing cost-effective solutions without compromising on quality. We leverage our extensive network of suppliers and partners to source materials and components.
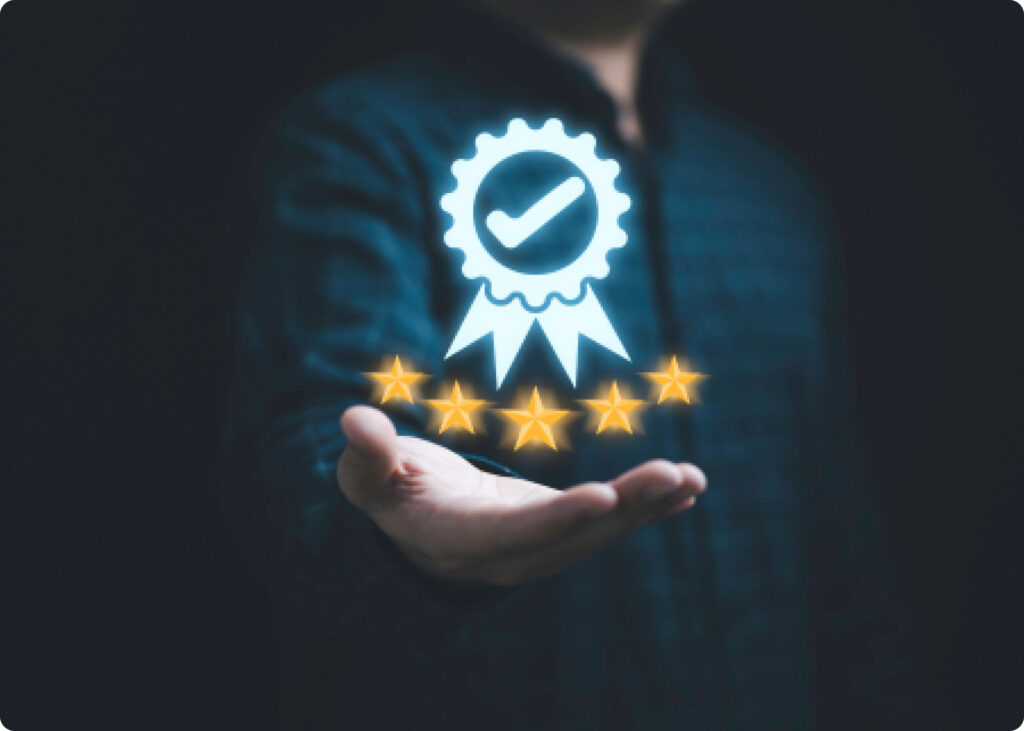
Technological Innovation

Customized Solutions
Every medical device project is unique, and TechFlex understands the importance of providing customized solutions that address specific patient needs. We take the time to understand these goals, challenges, and requirements, and tailor our services accordingly. This personalized approach ensures that our clients receive hardware solutions that are perfectly aligned with their objectives.
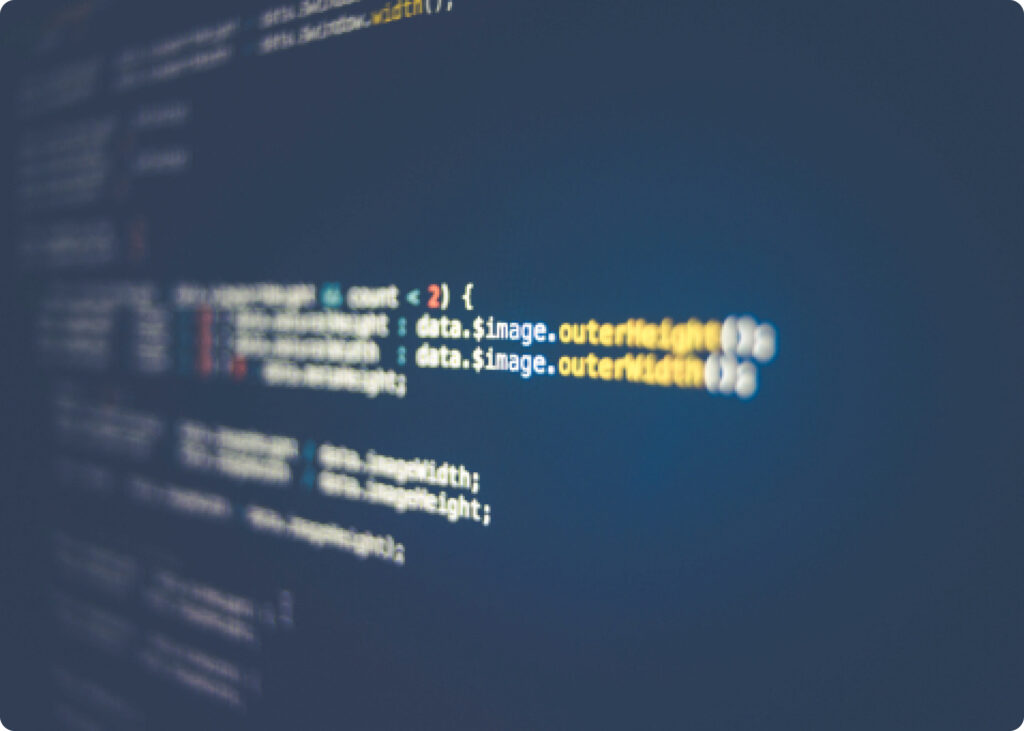
Sustaining Engineering
The relationship between TechFlex and our clients doesn’t end with the completion of the hardware development phase. We offer ongoing post-development support to ensure the continued success of our clients’ devices. This includes failure analysis and end of life updates. Our commitment to long-term support helps clients maintain the performance and reliability of their systems over time.
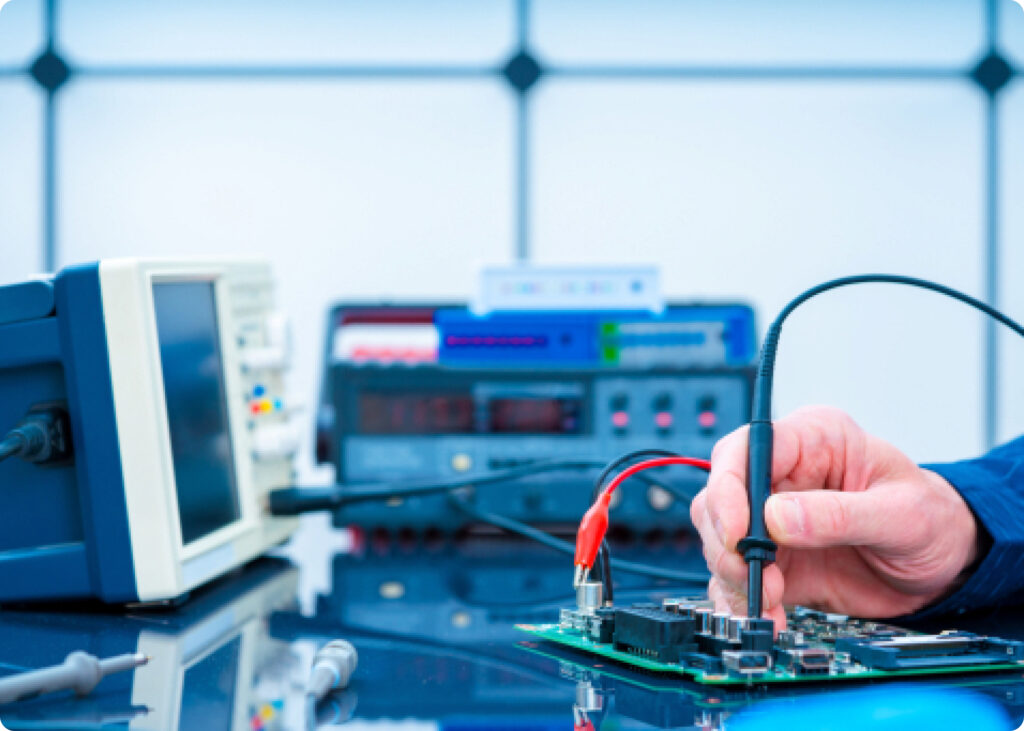
Proven Track Record
TechFlex has a proven track record of success in the medical device industry. Our portfolio includes a wide range of projects, from small-scale innovations to large, complex systems. Clients can rely on our experience and expertise to deliver high-quality solutions that meet their needs and exceed their expectations.

We offers a comprehensive suite of benefits and advantages for clients seeking engineering services in the medical device development sector. Rest assured that they are working with a team dedicated to delivering exceptional results and driving the success of their projects.